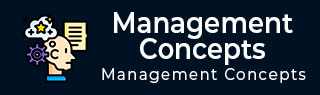
- 项目管理概念
- 项目管理主页
- 基于活动的成本核算
- 敏捷项目管理
- 基本管理技能
- 基本质量工具
- 基准测试流程
- 因果图
- 变更管理流程
- 通讯拦截器
- 沟通渠道
- 沟通方式
- 沟通模式
- 通讯管理
- 冲突管理
- 危机管理
- 关键链调度
- 关键路径法
- 做决定的过程
- 实验设计
- 有效的沟通技巧
- 有效的演讲技巧
- 企业资源规划
- 事件链方法论
- 极限项目管理
- 甘特图工具
- 准时制造
- 知识管理
- 超前、滞后和浮动
- 管理最佳实践
- 管理风格
- 目标管理
- 蒙特卡罗分析
- 动机理论
- 谈判技巧
- 组织架构
- PERT估计技术
- PRINCE2 项目方法论
- 帕累托图工具
- 强大的领导能力
- 基于流程的管理
- 采购文件
- 采购管理
- 项目活动图
- 项目章程
- 项目合同类型
- 工程成本控制
- 项目启动会议
- 项目经验教训
- 项目管理方法
- 项目管理办公室
- 项目管理流程
- 项目管理工具
- 项目管理三角
- 项目经理的目标
- 项目组合管理
- 项目质量计划
- 项目记录管理
- 项目风险类别
- 项目风险管理
- 项目范围定义
- 项目选择方式
- 项目成功标准
- 项目时间管理
- 项目劳动力管理
- 项目管理软件
- 质量控制和质量保证流程
- RACI 图表工具
- 认可和奖励
- 需求收集
- 资源平衡
- 人员配备管理计划
- 利益相关者管理
- 工作说明书 (SOW)
- 压力管理技巧
- 结构化头脑风暴
- 接班人计划
- 供应链管理
- 团队建设计划
- 团队激励
- 平衡计分卡
- 光环效应
- 自制还是外购的决定
- 七法则
- 虚拟团队
- 全面生产维护
- 全面质量管理
- 传统项目管理
- 工作分解结构
- 有用的资源
- 管理理念 - 快速指南
- 管理理念-资源
- 管理理念-讨论
全面生产维护
介绍
全面生产维护(TPM)是维护活动的概念。在结构上,全面生产维护类似于全面质量管理(TQM)的许多方面,例如员工授权、管理层的承诺、长期目标设定等。
此外,员工对其任务和职责的心态变化是两者之间的其他相似之处之一。
维护是任何组织的关键方面之一。当涉及到维护时,它可以代表业务组织内的许多领域和领域。
为了使组织正常运转,每个运行流程、活动和资源都应适当维护其质量、有效性和其他生产力因素。
TPM 是将组织的维护方面置于聚光灯下的过程。尽管传统管理方法将维护视为非盈利活动,但TPM却对其施加了限制。
随着对 TPM 的重视,维护停机已成为制造或生产过程本身不可或缺的一部分。现在,维护活动已得到妥善安排并按有组织的计划执行。
当生产要求较低或生产线中的物料流量较低时,维护事件不再被挤压。
通过实施 TPM,组织可以避免生产意外中断并避免计划外维护。
历史
TPM的母体是TQM。TQM 是在第二次世界大战后日本对质量问题产生关注后发展起来的。
作为全面质量管理的一部分,对工厂维护进行了检查。尽管 TQM 是组织最好的质量方法之一,但某些 TQM 概念在维护领域并不适合或无法正常工作。
因此,有必要开发一个单独的实践分支,以解决与维护相关的独特条件和问题。这就是作为 TQM 的子项引入 TPM 的方式。
尽管TPM的起源背后有一个故事,但起源本身却受到多方争议。
有人认为TPM的概念是由美国制造商在大约四十年前引入的,而另一些人则认为TPM是由日本汽车电气设备制造商引入的。无论起源如何,TPM 现在都可以在全球范围内使用。
实施
在开始为组织实施 TPM 概念之前,组织的员工应该确信高层管理人员对 TPM 的承诺。
这是在组织中建立良好 TPM 实践的第一步,如下所示。

为了强调上层管理人员的承诺,组织可以任命一名 TPM 协调员。,然后协调员有责任对员工进行 TPM 概念教育。
为此,TPM 协调员可以提出内部设计或从组织外部聘请的教育计划。通常,为了在组织中建立TPM概念,需要很长时间。
一旦协调员确信员工已做好准备,“研究和行动”小组就会开始执行。这些行动团队通常包括直接处理维护问题的人员。
机器操作员、轮班主管、机械师和高层管理代表也可以加入这些团队。通常,协调员应领导每个团队,直到选择团队领导为止。
然后,“学习行动”小组被赋予各自领域的职责。团队应该分析问题领域并提出一系列建议和可能的解决方案。
在研究手头的问题时,有一个并行进行的基准测试过程。在基准测试中,组织确定了为行业中某些机械和流程定义的某些生产力阈值。
一旦确定了纠正问题的适当措施,就应该将其付诸实践。作为一项安全措施,这些措施仅适用于生产线上的一个区域或一台机器。
这是一个试点计划,TPM 团队可以在不损害整个公司生产力的情况下衡量结果。如果结果成功,则相同的措施将应用于下一组机器或区域。通过遵循增量流程,TPM 可以最大限度地减少任何潜在风险。
结果
大多数世界一流的制造公司都将 TPM 作为其组织中的综合实践。福特、哈雷戴维森和达纳公司只是值得一提的几个例子。
所有这些一流的企业公民都表示,在实施 TPM 后,生产力得到了大幅提高。作为基准,几乎所有采用 TPM 的公司都报告在许多领域的生产力提高了近 50%。
结论
如今,随着竞争的加剧和市场的严峻,TPM可能决定一个公司的成败。TPM 多年来一直是一个经过验证的计划,组织(尤其是制造业组织)可以毫无风险地采用这种方法。
在 TPM 推出时,员工和高层管理人员应该接受 TPM 教育。组织应对 TPM 制定长期目标。